Consumables
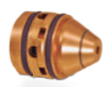
Nozzle
Focuses the gas and in turn the plasma arc down to the workpiece. Is the positive (+) electrical connection when forming the pilot arc which transitions to the material being cut once the arc is established.
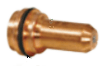
Electrode
Typically made up of mostly copper and has either a hafnium or tungsten tip. It receives electrical current from the negative (cathode) connection inside the torch. Focuses the charge through its tip initiating an arc first with the nozzle (pilot arc) and subsequently onto the workpiece for cutting.
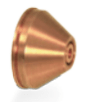
Shield Cap
Protects the torch and the components inside from molten metal ejection, sparks, excess heat and wayward arcs. Also concentrates the shield gas during cutting.
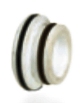
Swirl Ring or Plasma Distributor
Sits between the electrode and the tip. Its purpose is to evenly distribute the plasma gas and to induce the swirling action in the gas, surrounding the plasma arc for greater precision, straighter single side cutting and lastly to evenly cool preceding components with the gas distribution.
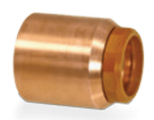
Shield Gas Distributor
Works in combination with the swirl gas ring to produce a more stabilized arc and straighter cut edge quality. Directing the plasma shield gas around the plasma arc.
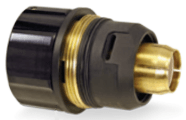
Cartridge
Connects consumable stack to the torch, provides the electrical interface between torch and the stack.
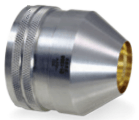
Shield Cup
Works in combination with the swirl gas ring to produce a more stabilized arc and straighter cut edge quality. Directing the plasma shield gas around the plasma arc.
Frequently Asked Questions
How often do I change my plasma consumable?
The frequency at which you need to change out consumables will vary depending on a few factors, including:
- What you are typically cutting, material and thicknesses
- Amperage
- Speed of cutting
- Torch height
- Gas Quality
- The number of pierces accumulated
Considering the last variable, number of pierces, reducing this number by edge starting a sheet and connecting your cut-outs together as if it were one continuous cut path will greatly improve the mileage you get out of your electrode and nozzles.
How do I know when my consumables need changing?
First off visually check your consumables if you experience a noticeable change in cutting results. This could include:
- Increased dross accumulation
- Abnormal high degrees of bevel angle (in non-bevel cutting, of course)
- Inconsistent piercing results
Second, the sound the torch is making during cutting changes from a consistent higher pitch sound to a fluctuating or inconsistent noise. Many experience operators and technicians can tell by ear if the plasma isn’t operating at optimal conditions.
Lastly, a quick check in your table manufacturers software; where many will tell you how many pierces have been completed on a set of consumables. Additionally, some will include compensation for worn components, increasing the pierce duration to make sure complete penetration is made.
What causes plasma consumables to wear?
As discussed above, the number of pierces will have the most detrimental affects on the consumable stack. Many plasma manufacturers will provide estimate numbers of pierces that the electrode – nozzle pairing will produce.
How do I know if my consumables are bad?
Visual checks are your best bet to determine the state of the consumable items. In additional to the performance decreases explained above. Here is a quick reference for what to look for when determining if each consumable item is no longer good to use:
- Nozzle – enlarge orifice and irregular shaped hole (non-circular and material blasted or worn away)
- Electrode – hafnium (or tungsten) tip worn away, large craters observable in tip
- Shield Cap – plugged gas holes, excess slag that is too heavy to clean away